Uddeholm Dievar
– setzt neue Maßstäbe!
Es liegt in der Natur des Menschen, sich nicht auf „unbekanntes Terrain“ zu
wagen und Gewohnheiten nicht zu ändern – warum auch sollte man auf
Altbewährtes verzichten?
Aber wenn wir niemals versuchen, unsere Komfortzone zu verlassen,
gäbe es keinen Fortschritt. Wir bei Uddeholm glauben an kontinuierliche
Verbesserung und Weiterentwicklung. Daher sind wir in der Lage, einen
Warmarbeitsstahl herzustellen, der in Bezug auf Zähigkeit und Leistung
völlig neue Maßstäbe setzt: Uddeholm Dievar 25 Joule!
Diese neue Werkzeugstahl-Entwicklung von Uddeholm bietet ein perfektes
Verhältnis zwischen Zähigkeit und Brandrissbeständigkeit für den
Aluminium-Druckguss und andere Anwendungen.
Uddeholm Dievar besitzt sowohl eine hohe Zähigkeit, als auch eine hohe
Warmfestigkeit. Daher bietet er Ihnen als Kunde folgende Vorteile:
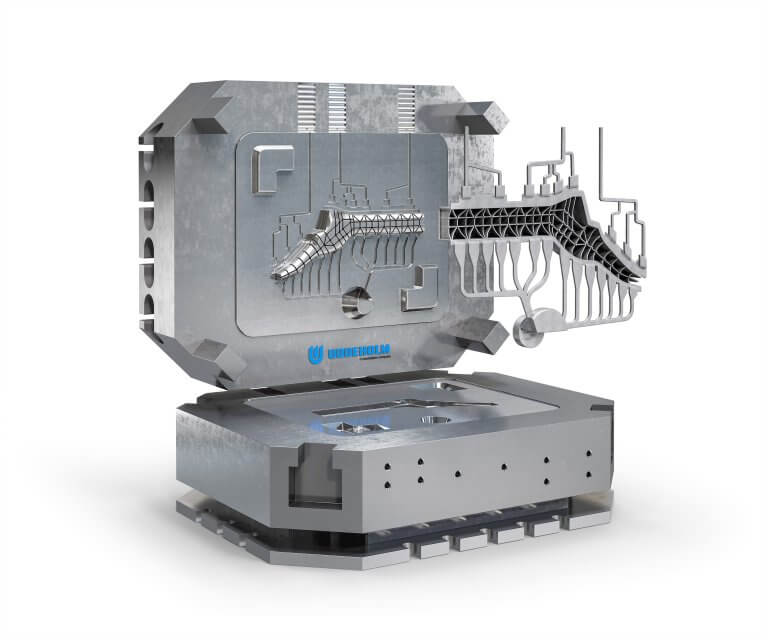
Viele unserer Kunden werden sagen, Uddeholm Dievar ist doch nicht neu. Dies stimmt nur bedingt. Der Herstellungsprozess von Uddeholm Dievar wurde
im Laufe der Zeit optimiert, wodurch dieser zäher wurde. Parallel dazu, sind bei den Druckgießern die Anforderungen gestiegen.
Dieser Trend besteht insbesondere bei neuen Gussteilen, speziell bei Teilen für die E-Mobilität und für Strukturbauteile. Hier kommt der Oberflächenqualität
eine besondere Bedeutung zu. Die Zeit ist also reif für eine Veränderung – für den neuen Uddeholm Dievar mit einer garantierten Kerbschlagarbeit von
25 Joule nach den Regeln der strengen Lieferrichtlinie der NADCA. Diese Lieferrichtlinie wurde von der NADCA geändert und Uddeholm Dievar bildet
eine eigene Spitzenkategorie, die kein anderer Warmarbeitsstahl erreicht. Uddeholm Dievar setzt neue Maßstäbe!
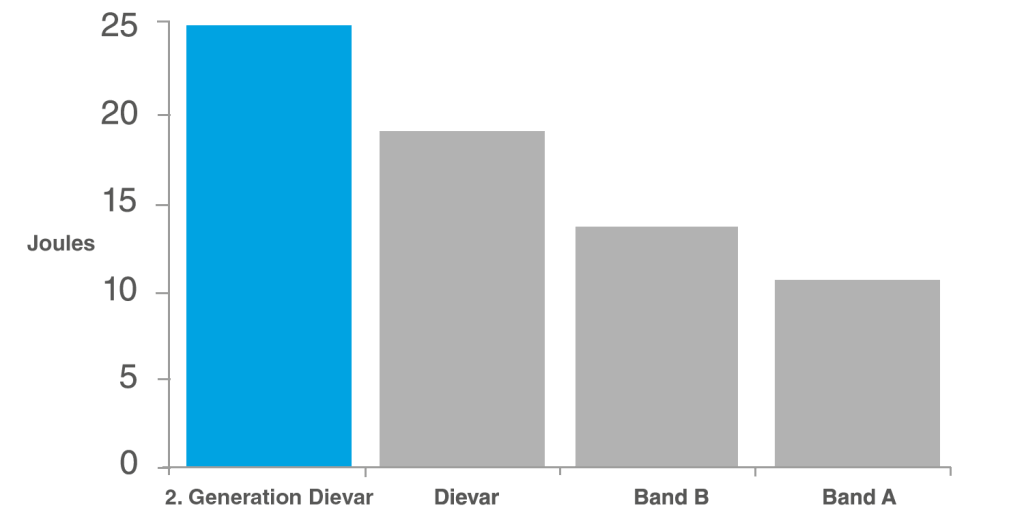
Warum aber wählen die meisten Formenbauer, Gießereien und
OEMs für den Druckguss nach wie vor die Werkzeugstahlqualitäten
1.2343 oder 1.2344, obwohl Uddeholm Dievar deren Leistung bei
Weitem überragt?
Erstaunlicherweise stammen diese beiden Qualitäten aus der Mitte
des letzten Jahrhunderts. Können diese Stähle dem Vergleich
mit Uddeholm Dievar wirklich standhalten, wenn es darum geht,
die größten Probleme der Werkzeuganwender von heute zu lösen?
Herausforderungen von Strukturbauteilen meistern
Um die oben stehenden Fragen zu beantworten, müssen wir zunächst klären, aus welchen Gründen Formeinsätze für den Automobilbau am häufigsten
ausfallen. Es gibt bei Druckgussformen überwiegend vier Ausfallmechanismen: Erosion, Metallkorrosion, Brandrissbildung und Spannungsrisse bzw.
Formbrüche. Die Brandrissbildung macht dabei erfahrungsgemäß den größten Anteil aus. Dieser Versagensmechanismus variiert von Gießerei zu
Gießerei, repräsentiert jedoch im Durchschnitt rund 80 % der Fälle, während die übrigen 20 % auf die anderen Ausfallursachen entfallen.
Die durchschnittlichen Kosten für das „Handverputzen“ der Druckgussteile aus der Form mit den Einsätzen aus 1.2343 ESU beliefen sich auf circa 0,97 € pro Teil. Daraufhin wurde die nächste Form mit Einsätzen aus dem Premium-Warmarbeitsstahl Uddeholm Dievar hergestellt. Die Druckgussform hat aktuell 26.000 Teile produziert und weist keine Risse auf und einen äußerst geringen Verschleiß auf. Um den Kostenvorteil abschätzen zu können, haben wir für die Kalkulation der durchschnittlichen Kosten für das „Handverputzen“ der Druckgussteile aus der Dievar-Form bis zum Standzeitende 0,40 € pro Teil angenommen, obwohl die Kosten vermutlich niedriger ausfallen werden. Mögliche höhere Standzeiten der Form und vermutlich geringere Instandhaltungskosten wurden in der Berechnung nicht einbezogen. Dennoch sind die Einsparungen beträchtlich:
Warum ist das so? Wenn wir den abgebildeten Längsträger und die dazugehörige
Form betrachten, können wir feststellen, dass diese eine sehr große Oberfläche
mit vielen dicken und dünnen Abschnitten hat. Da diese Gussteile sicherheits-
relevant sind, sind Porosität und andere interne Gießfehler zu vermeiden. Dies
erfordert eine möglichst schnelle Füllung der Form. Damit die Anschnittge-
schwindigkeit dabei nicht zu hoch wird, hat ein typisches Strukturteil wesentlich
mehr Angüsse als ein herkömmliches Teil aus dem Antriebsstrang – in diesem
Beispiel 14 Stück.
In den Anschnitten wird zusätzliche Wärme erzeugt. In Verbindung mit den
allgemeinen Erwärmungs- und Abkühlungsvorgängen im Gießzyklus sowie dem
Sprühprozess kann es zu starker Brandrissbildung kommen. Aufgrund der
Sicherheitsrelevanz vieler Strukturbauteile müssen diese frei von potenziellen
Rissauslösern mit Kerbwirkung sein. Potenzielle Rissauslöser können Brandrisse
sein. Weiterhin müssen sie mit anderen Teilen verbunden werden können.
Brandrisse in den Fügezonen sind häufig unzulässig. Da das flüssige Aluminium
die Formoberfläche sehr gut abbildet, zeigt sich die Schädigung der Form auch
am gegossenen Teil.
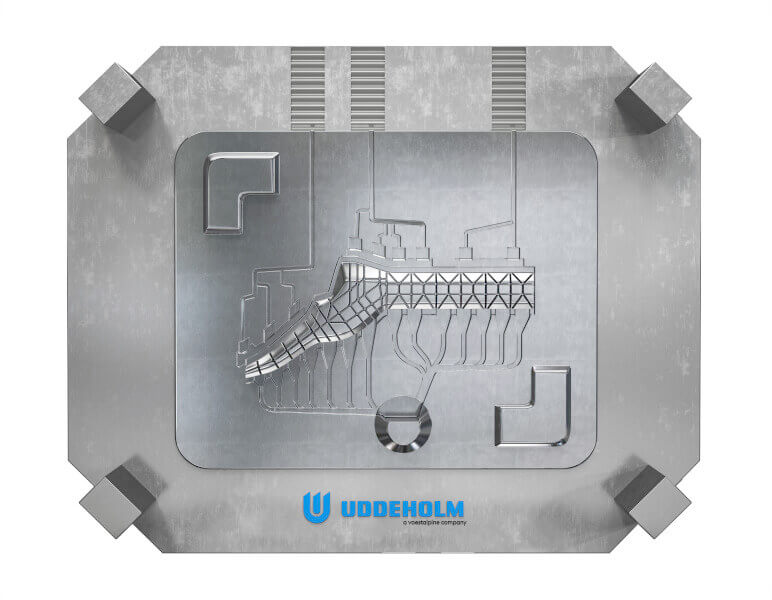
Liegt die Grathöhe außerhalb der Toleranz, muss das Teil geputzt, der Einsatz repariert oder ein neuer Einsatz gebaut werden. Dies alles
verursacht erhebliche Kosten und senkt die Margen. Zudem geht der Trend zu größeren Druckgussteilen und somit größeren Formen.
Was einher geht mit einem größeren Risiko von Spannungsrissen. Der gewählte Warmarbeitsstahl muss daher zusätzlich sehr zäh und
duktil sein.
Uddeholm Dievar, eine optimierte Lösung gegen Brandrissbildung
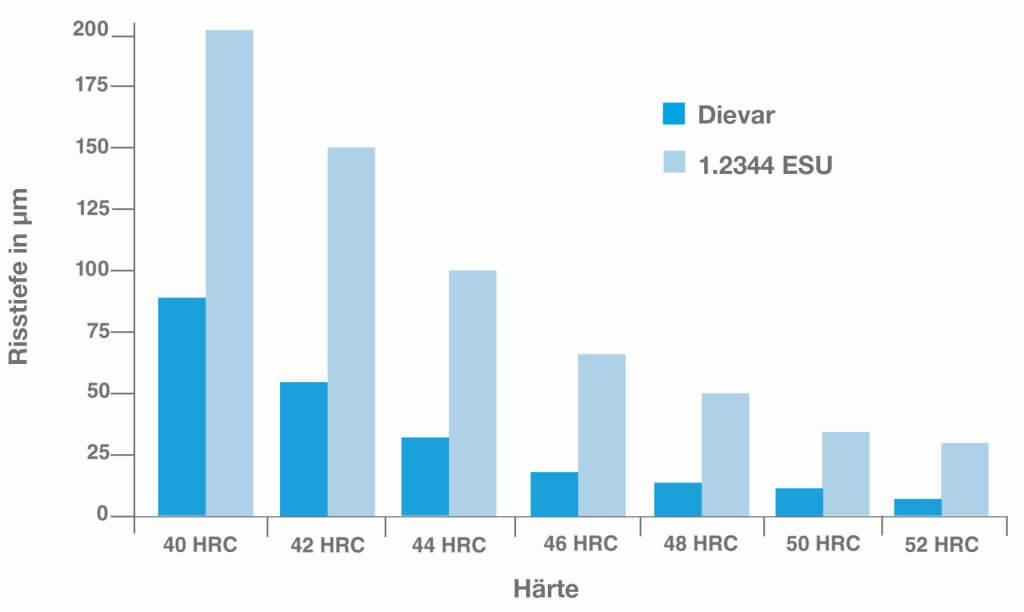
Dem Feedback von unseren Kunden und Fallstudien zufolge liefert
Dievar im Vergleich zu den Warmarbeitsstählen 1.2343 ESU und
1.2344 ESU ausgezeichnete Ergebnisse, wenn Brandrisse die
Hauptausfallursache darstellen.
Dies wird auch durch Thermoschockversuche bestätigt:
Wie im Diagramm zu sehen ist, sind die Risse im 1.2344 ESU
bei gleicher Härte wesentlich tiefer als im Dievar.
Uddeholm Dievar ist 1.2343 und 1.2344 in ESU-Premium-Qualität
in allen wichtigen Stahleigenschaften überlegen.
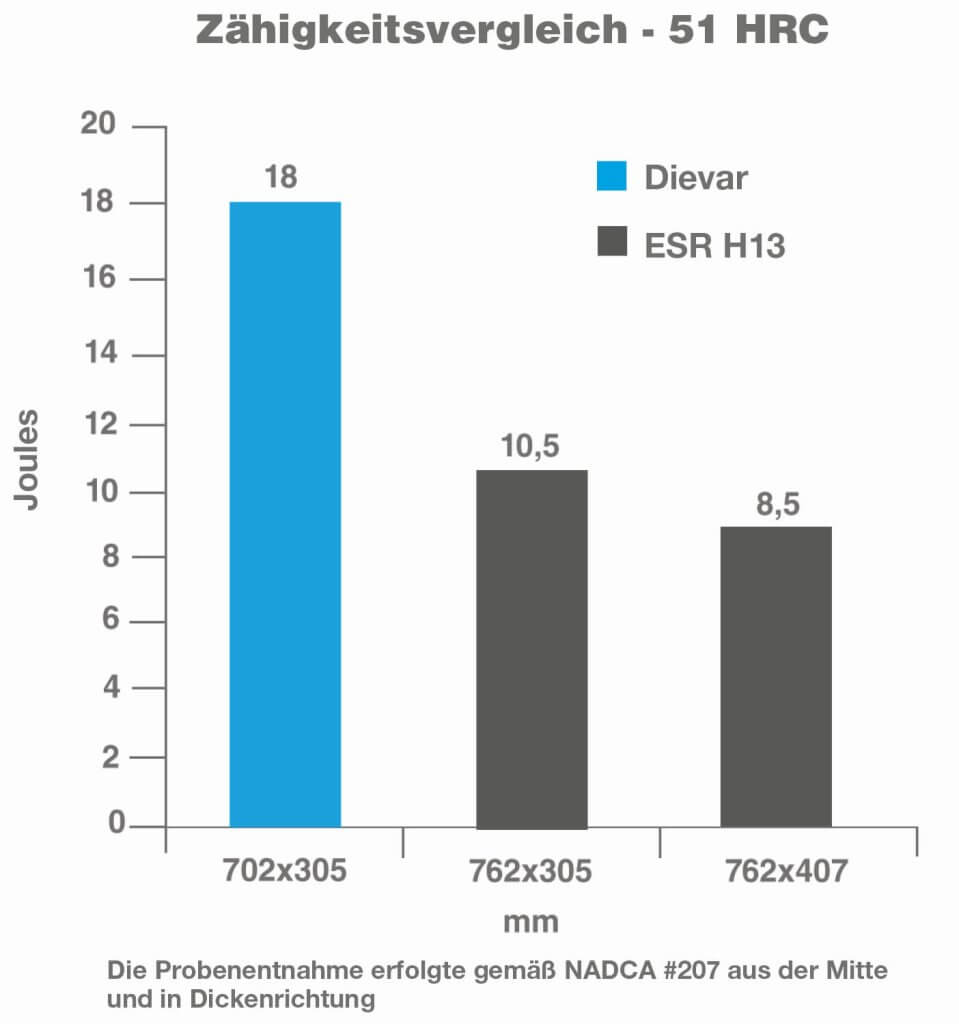
Besonders herauszuheben sind die Zähigkeit und die Duktilität.
Uddeholm Dievar bietet dem Druckgießer mit einem Mindestdurchschnittswert
von 25 Joule Schlagzähigkeit (Charpy-V-Probe nach NADCA-Richtlinie) eine
hohe Produktionssicherheit. Diesen Wert garantieren wir unabhängig von der
Blockgröße.
Eine hohe Duktilität ist ebenfalls wichtig, da sie die Risseinleitung
bei der thermischen Ermüdung verzögert. Jüngste Prüfungen ergaben für
Uddeholm Dievar bei 44 bis 46 HRC eine Schlagbiegearbeit von über 400 Joule
(ungekerbte Probe). Hohe Duktilität und Zähigkeit ermöglichen auch die
potenzielle Erhöhung der Härte der Einsätze, da eine höhere Härte bekannter-
maßen zu einer besseren Brandrissbeständigkeit beiträgt.
Auf Kundennachfrage wurde der neue Dievar oberhalb der Standardhärte von
44 – 46 HRC getestet. Ergebnis war, dass Uddeholm Dievar selbst bei 51 HRC
die Zähigkeit von 1.2344 ESU übertrifft. Die Charpy-V-Proben stammten aus
Blöcken von vergleichbarer Größe.
Wenn Sie planen, die Härte eines Einsatzes oder einer Form zu erhöhen, empfehlen wir Ihnen zunächst Rücksprache mit einem Uddeholm-Techniker zu halten. Mit unserem Gesamtpaket aus der 2. Generation Uddeholm Dievar, optimierten Wärmebehandlungsprozessen und unserer ausgewiesenen Expertise im Druckguss sind wir bereit, mit Ihnen gemeinsam die Herausforderungen neuer Gussteile zu meistern.