Additive Fertigung für Kaltarbeitsstähle?
Vanadis 4 Extra SuperClean für EBM!
Die additive Fertigung von Metallen entwickelt sich immer mehr zu einer etablierten Technologie für die Herstellung von Werkzeugen im Kunststoff-Spritzguss. Viele Unternehmen nutzen die additive Fertigung, um Kosten zu sparen und die Produktivität durch kürzere Zykluszeiten zu erhöhen.
Der Markt für additiv gefertigte Werkzeuge in Warmarbeitsanwendungen, wie z. B. Einsätze in Druckgussformen, wächst ebenfalls. Hier wird jedoch eher gießtechnischen Problemen, wie ungewollter Porosität oder Schrumpfung, entgegengewirkt, indem die Erstarrungsbedingungen der Gussteile durch additiv gefertigte Einsätze mit komplexer Kühlung optimiert werden.

Für Kaltarbeitswerkzeuge steckt die AM-Technologie dagegen noch in den Startlöchern. Im Automotive-Bereich werden angesichts der steigenden Nachfrage nach immer leichteren Produkten viele hochfeste Stahlbleche verwendet. Die Bearbeitung dieser Bleche stellt besondere Anforderungen an den Werkzeugstahl, der zum Stanzen, Schneiden oder Umformen eingesetzt wird. Die wichtigsten Eigenschaften von Kaltarbeitsstählen sind eine ausgezeichnete Verschleißbeständigkeit bei gleichzeitig hoher Duktilität bzw. Bruchsicherheit. Die Verschleißbeständigkeit wird durch quasi-keramische Teilchen, sogenannte Karbide, erreicht, die innerhalb des gehärteten und angelassenen Stahlgefüges vorliegen. Die Entstehung von Karbiden wird durch einen hohen Kohlenstoffgehalt in Kombination mit weiteren Legierungselementen gezielt gesteuert. Der hohe Legierungsgehalt erschwert jedoch die Herstellung von Kaltarbeitsstählen mittels additiver Fertigung. Das Hauptproblem liegt in der Rissanfälligkeit bei der schnellen Erstarrung der aufgeschmolzenen Pulverpartikel. Aus demselben Grund gelten hochlegierte Kaltarbeitsstähle als schwer bis nicht-schweißbar.
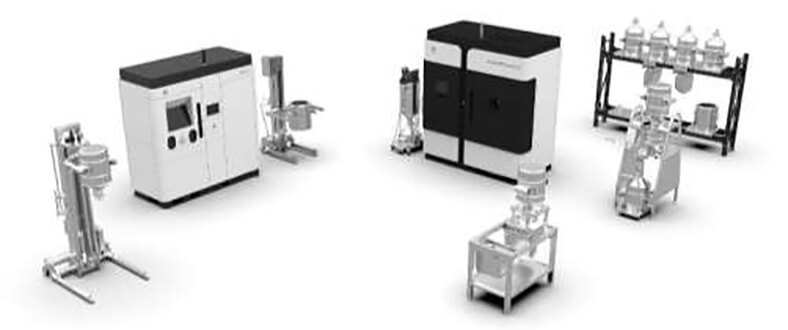
Zur Vermeidung der Rissproblematik während der additiven Fertigung muss eine Vorwärmung des Pulvers auf eine hohe Temperatur durchgeführt werden. Die Durchwärmung muss bei dem sukzessiv aufgebauten Bauteil jedoch sehr gleichmäßig erfolgen.
Diese Prozessführung kann mit den meisten Laser-Pulverbett-Maschinen nicht realisiert werden. Der Einsatz des Elektronenstrahlschmelzverfahrens (EBM) bietet dagegen neue Möglichkeiten für die additive Fertigung von Kaltarbeitsstählen.
EBM ist ein spezielles additives Fertigungsverfahren, bei dem der Elektronenstrahl sowohl zum Durchwärmen als auch zum Schmelzen eingesetzt werden kann. Dadurch kann die Temperatur während des Druckvorgangs konstant gehalten und die Rissbildung verhindert werden.
Weiterhin handelt es sich bei der EBM-Technologie um ein Vakuumverfahren, wodurch ein hoher Schutz vor Verunreinigung am Pulver vorliegt. Die präzise Prozesssteuerung stellt sicher, dass die chemische Zusammensetzung des Werkstoffes innerhalb der Spezifikation verbleibt. Hohe Erstarrungsraten beim Schmelzen führen zu einem feinen und homogenen Gefüge, das sowohl für die Karbidbildung als auch für deren gleichmäßiger Verteilung notwendig ist.
(Bild rechts: Uddeholm Vanadis 4 Extra – Verarbeitung bei 950°C)
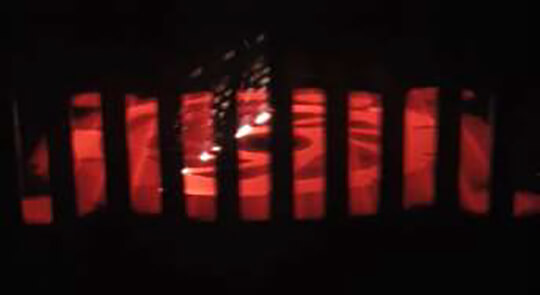
Zur Vermeidung der Rissproblematik während der additiven Fertigung muss eine Vorwärmung des Pulvers auf eine hohe Temperatur durchgeführt werden. Die Durchwärmung muss bei dem sukzessiv aufgebauten Bauteil jedoch sehr gleichmäßig erfolgen. Diese Prozessführung kann mit den meisten Laser-Pulverbett-Maschinen nicht realisiert werden. Der Einsatz des Elektronenstrahlschmelzverfahrens (EBM) bietet dagegen neue Möglichkeiten für die additive Fertigung von Kaltarbeitsstählen.
Um das Potenzial von EBM für Kaltarbeitsstähle zu erschließen, hat Uddeholm das Pulver „Uddeholm Vanadis 4 Extra SuperClean für EBM” entwickelt. Uddeholm Vanadis 4 Extra SuperClean ist ein Chrom-Molybdän-Vanadium-legiertes Stahlpulver, das für Premium PM-Stähle entwickelt wurde und nun für das EBM-Verfahren in modifizierter Ausführung vorliegt. Die hervorragenden Materialeigenschaften der PM-Variante werden beibehalten. Durch die richtigen Prozessparameter bei der EBM-Herstellung und der nachfolgenden Wärmebehandlung ist es möglich, ein gehärtetes Gefüge mit fein verteilten Vanadiumkarbiden zu erzielen, das ausgezeichnete Verschleißeigenschaften in Verbindung mit einer guten Zähigkeit aufweist. Die Härte von Bauteilen aus „Uddeholm Vanadis 4 Extra SuperClean für EBM” liegt bei 64 HRC mit einer Druckfestigkeit von 2700 MPa und einer Zähigkeit von 20 J. Das mittels EBM gedruckte Werkzeug wurde auch bei Stanz- und Prägevorgängen getestet. Sowohl die Verschleißeigenschaften des Werkzeugs als auch die Qualität der hergestellten Teile sind sehr ähnlich zum Vanadis 4 Extra SuperClean PM-Stahl.

Die Vorteile der additiven Fertigung von Kaltarbeitsstählen liegen in der Reduktion des mechanischen Bearbeitungsaufwands. Bei der klassischen Fertigung komplexer Werkzeuge müssen teilweise bis zu 75% des Werkstoffes durch spanabhebende Verfahren entfernt werden. Mit gedruckten Kaltarbeitsstählen können somit Zeit, Kosten als auch Energie eingespart werden. Bei besonders zeitkritischen Aufträgen kann die additive Fertigung somit eine gute Ergänzung zum traditionellen Werkzeugbau sein, um Werkzeuge mit vergleichbaren Eigenschaften wie herkömmliche Werkzeuge zu drucken. Es gibt also definitiv Kaltarbeitsanwendungen, bei denen die additive Fertigung eine interessante Option bzw. eine wettbewerbsfähige Lösung sein kann, sowohl aus technologischer als auch aus finanzieller Sicht.