Innovative Schmelzefilter aus dem 3D-Drucker
flow filter V und flow filter X gedruckt aus Uddeholm Corrax!
Mit den Schmelzefiltern flow filter V und flow filter X hat die voestalpine High Performance Metals Division am Standort Düsseldorf ein einfaches Standardprodukt für den Kunststoffspritzguss neu erfunden. Mit Hilfe modernster 3D-Druck-Technologie und der damit verbundenen Freiheitsgrade im Design wurden innovative Schmelzefilter entwickelt, die ihre konventionell hergestellten Alternativen weit hinter sich lassen.
Recycling von Kunststoffen ist ein wichtiger Baustein auf dem Weg zu einer nachhaltigeren Produktion von Konsumgütern und Verpackungen und somit zu einer saubereren Umwelt. Heutzutage ist der Anteil an recyceltem Material bei der Herstellung neuer Kunststoffteile allerdings noch gering. Vor dem Hintergrund von jährlich rund 400 Millionen Tonnen CO2, die durch weltweite Herstellung und das Verbrennen von Kunststoffen emittiert werden, ist mehr Nachhaltigkeit dringend erforderlich. Da wundert es nicht, dass der weltweit größte Spielzeughersteller verkündet, an Prototypen für Kunststoff-Spielsteine zu forschen, die zu 100% aus recyceltem Material bestehen.
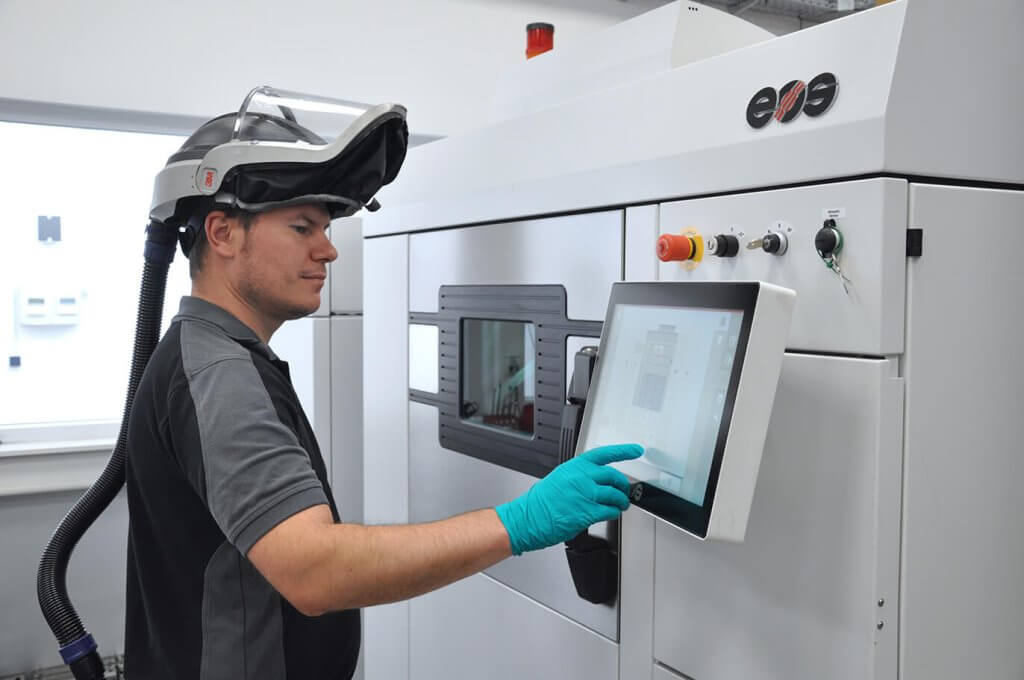
Recycelter Kunststoff ist für den Spritzgießer ein herausfordernder Rohstoff. Problematisch sind vor allem Verunreinigungen, die im Wiederaufbereitungsprozess ins Arbeitsmaterial gelangen. Verunreinigungen können einerseits die Teilequalität negativ beeinflussen, andererseits besteht die Gefahr, dass enge Anspritzpunkte verstopfen und der Produktionsprozess zum Erliegen kommt. Aufwendige Reinigung, Produktionsausfall und Mehrkosten durch Instandsetzung sind die Folge.
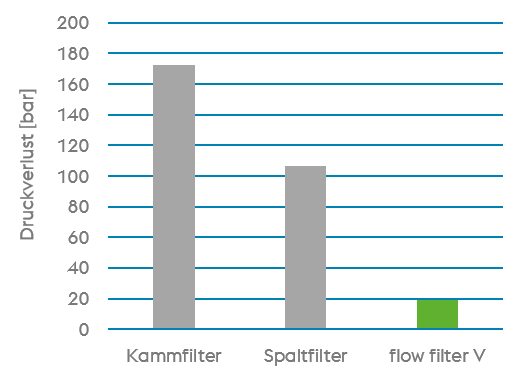
Hoher Druckverlust bei konventionellen Filtern
Um diesen Gefahren entgegenzuwirken, können Schmelzefilter in die Maschinendüse eingesetzt werden. Es handelt sich hierbei um mechanische Siebe, die in verschiedenen Ausführungen auf dem Markt erhältlich sind. Viele Spritzgießer scheuen sich vor dem Einsatz von Schmelzefiltern.
Hauptgrund ist oftmals ein hoher Druckverlust, den diese Filter bewirken. Druckverlust kann zu Problemen bei der Formfüllung, Qualitätseinbußen, höherem Energieverbrauch und schnellerem Maschinenverschleiß führen.
Dazu kommt, dass viele Filter den Kunststoff mit einer starken Scherspannung belasten. Die zu Farbänderungen und reduzierten mechanischen Eigenschaften führen kann.
⇐ Exemplarische Messung des Druckverlustes.
Kunststoff ABS, Düsentemperatur 240°C, Einspritzgeschwindigkeit 75 cm3/s
Fairerweise sollte festgehalten werden, dass verfügbare Filtereinsätze für den Kunststoffspritzguss oft schon ein guter Kompromiss – bei der Abwägung von Reinigungswirkung und Fließverhalten auf der einen Seite und wirtschaftlicher Herstellbarkeit mit konventionellen Methoden auf der anderen Seite – sind. Doch was wäre, wenn es nicht mehr nötig wäre, Kompromisse beim Fertigungsverfahren einzugehen, und nur noch die Funktion des Bauteils im Vordergrund stünde?
Alles für den optimalen „flow“
Unter dieser Prämisse hat die voestalpine High Performance Metals Division in Düsseldorf Filtereinsätze designt, die nur vernachlässigbar in die Strömung des Kunststoffes eingreifen. Der flow filter V ist ein Produkt, das die Funktion kompromisslos in den Vordergrund stellt. Möglich macht dies die innovative Fertigung mittels 3D-Metalldruck. Die Designer konnten sich bei der Konstruktion voll und ganz auf die rheologische Auslegung, sprich den optimalen „flow“ der Kunststoffschmelze konzentrieren. Wie die vielen kleinen Filterelemente in die Struktur eingebracht werden können, stand nicht im Vordergrund ihrer Überlegungen. Denn schließlich wird für die Herstellung des flow filter V weder gebohrt noch gefräst, sondern lediglich das Pulver an den entscheidenden Stellen aufgeschmolzen und zu einem festen Körper verbunden.
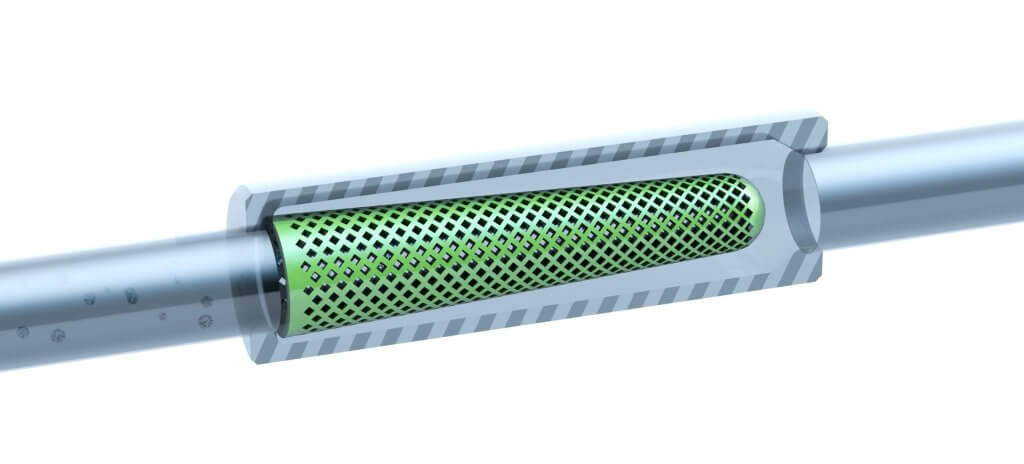
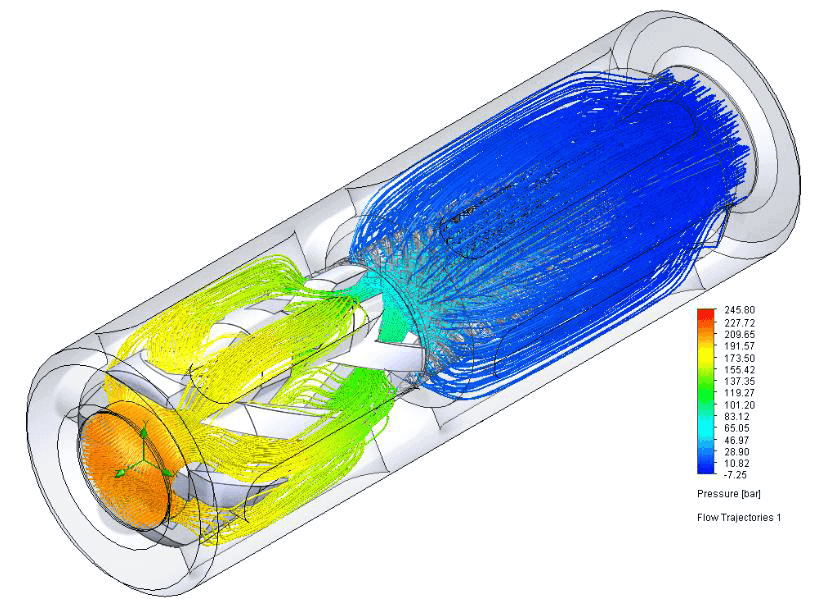
Die Konzentration auf den optimalen „flow“ zahlt sich voll aus. In allen Tests zeigen flow filter V wesentlich geringere Druckverluste im Vergleich zu häufig eingesetzten Standardfiltern (z. B Kamm- oder Spaltfiltern).
Dazu kommt, dass die Maschenweite des flow filter konstant niedrig bei 0,6 mm liegt, und zwar unabhängig vom Filterdurchmesser. Dies ist ein weiteres wesentliches Unterscheidungsmerkmal des flow filter V zu den bestehenden Lösungen.
Letztere weisen bei größeren Filterdurchmessern oft eine deutlich größere Maschenweite als kleinere Filter auf. Eine Notwendigkeit, um den Druckverlust im Rahmen zu halten was leidet, ist die Filterqualität. Der flow filter V hingegen bietet gleichbleibende Filterqualität in allen Durchmessern, bei konstant minimalem Druckverlust.
Neben dem flow filter V haben die 3D-Druck-Experten aus Düsseldorf einen zweiten Filter entwickelt, der weitere Kundenbedürfnisse bedient. Einige Anwendungen erfordern neben der Reinigung auch eine zusätzliche Durchmischung der Schmelze. Insbesondere wenn die Farbgebung des Kunststoffes erst an der Maschine, durch Zugabe von Masterbatches, erfolgt. Hier bilden sich schnell Schlieren im Kunststoffbauteil. Um dem entgegenzuwirken, vereint der flow filter X einen hocheffizienten Filter und einen statischen Mixer auf engstem Raum. Der Spritzgießer profitiert von guter Durchmischung der Schmelze und erhält gleichzeitig die höchste Sicherheit gegen Produktionsausfall durch verstopfte Anspritzpunkte. In Anwendungstests konnten bei laufendem Spritzbetrieb mit dem flow filter X bis zu 15 % Masterbatch eingespart werden. Bares Geld für den Spritzgießer.
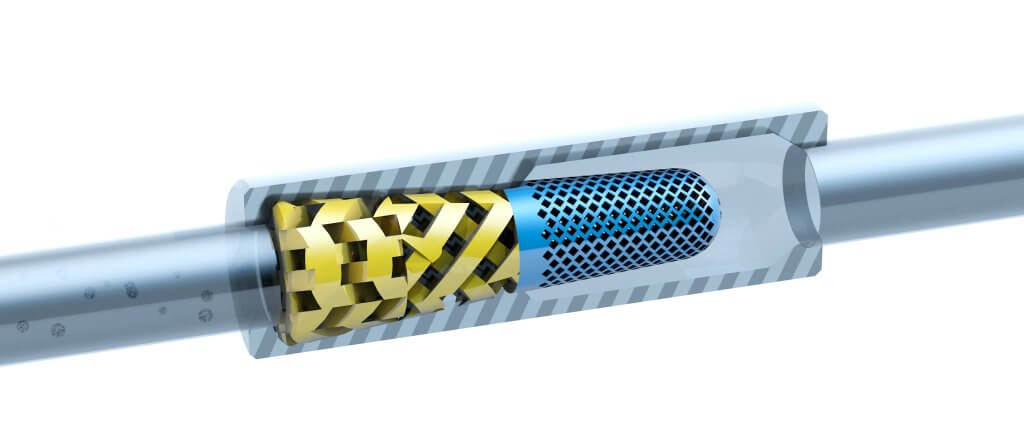
Bestes Pulver für beste Produkte
Die Expertise in der Strömungsmechanik, der die flow filter ihre herausragenden Eigenschaften zu verdanken haben, stammt aus dem voestalpine Additive Manufacturing Center in Düsseldorf. Die beteiligten Ingenieure haben sich ihre Erfahrungen in der Auslegung optimal fließender Kühlkreisläufe von Spritzgießwerkzeugen zu Nutze gemacht, um den flow filtern den richtigen „flow“ einzuhauchen.
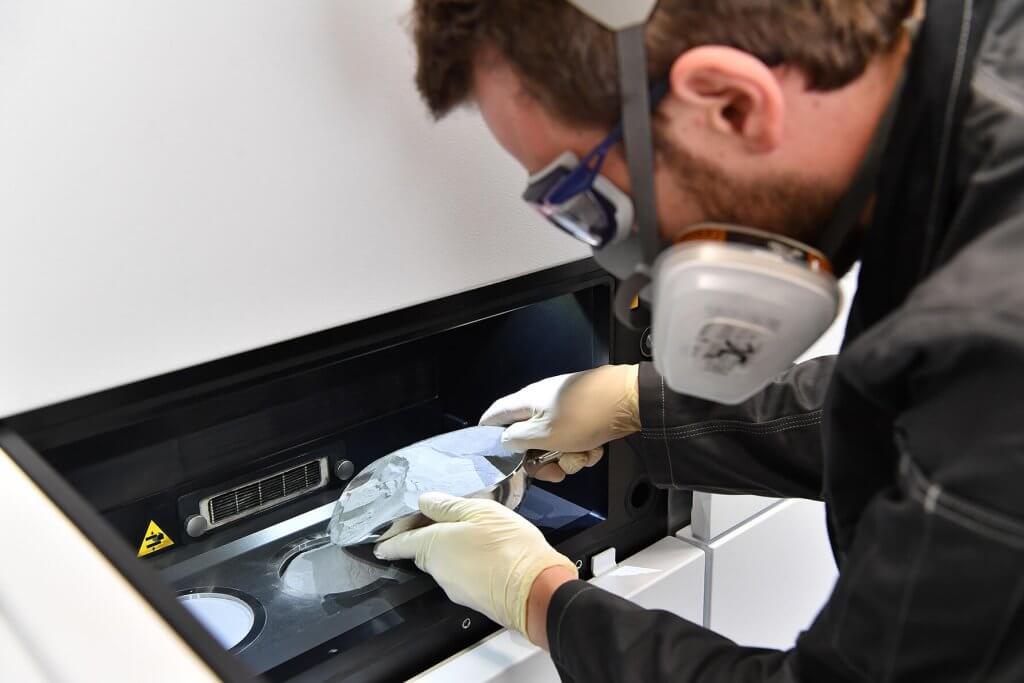
Darüber hinaus trägt die hohe Werkstoffkompetenz des Unternehmens zur Einzigartigkeit der Filter bei. Das zum Metalldruck der Bauteile eingesetzte Pulver Uddeholm Corrax stammt aus der hochmodernen Pulververdüsungsanlage des Stahlwerkes Uddeholms AB in Hagfors, Schweden.
Uddeholm Corrax verleiht den flow filtern durch seine herausragende Korrosionsbeständigkeit in Kombination mit sehr hoher Festigkeit und guter Verschleißfestigkeit eine besonders hohe Widerstandsfähigkeit und Langlebigkeit.
Die optimale Morphologie und Verarbeitbarkeit von Uddeholm Corrax Pulver führt zu höchster Replizierbarkeit und Produktqualität der Filter.
So viel Hightech müsste eigentlich einen hohen Verkaufspreis der flow filter zur Folge haben. Schließlich ist der 3D-Metalldruck immer noch ein vergleichsweise kostspieliges Fertigungsverfahren. Dem ist aber nicht so. Die Tatsache, dass die Filter mit wesentlich weniger Material gedruckt werden, als bei konventionellen Methoden abgetragen wird, macht die flow filter in den meisten Fällen sogar zur günstigeren Alternative.