Uddeholm Corrax für AM
– additive Fertigung einen Schritt weitergedacht
Zykluszeitreduzierung durch konturnahe Kühlung bei additiv gefertigten Spritzgusseinsätzen aus Uddeholm Corrax ist inzwischen in der Serienproduktion angekommen. Die Reduzierung des Ausschusses durch eine homogenere Kühlung ist heute ebenfalls Stand der Technik. Doch die additive Fertigung bietet weiteres Potenzial um die Wirtschaftlichkeit zu steigern.
Optimierte Topologie der additiv gefertigten Einsätze: Stellen Sie sich vor, Sie würden einen Einsatz konventionell (Drehen, Fräsen, Erodieren, … ) fertigen. Bei diesem Einsatz entfernen Sie nur das überschüssige Material. Jede weitere Bearbeitung, die keinen Mehrwert bietet, erhöht Ihre Fertigungskosten.
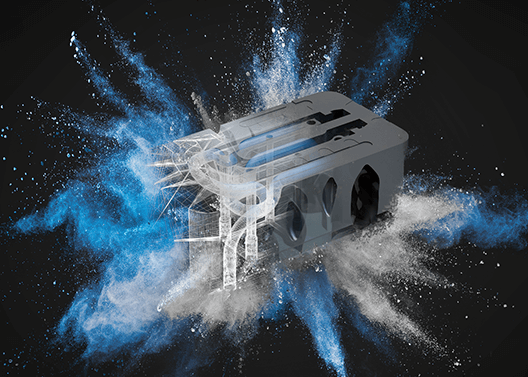
Wir haben diesen Gedanken auf die additive Fertigung übertragen. Wieso sollte ein massiver Block gefertigt werden, wenn andere Strukturen für die Belastungen ausreichend sind?
Aus diesem Grund haben wir die Belastung im Werkzeug simuliert und eine konstruktive Anpassung anhand bionischer Strukturen vorgenommen. Dies dient der Kostenreduktion, denn wieso sollten Pulver, Maschinenkosten und Zeit für Material investiert werden, die nicht benötigt werden?
So wie man konventionell kein weiteres Material aus einem Block entfernen würde, lohnt es sich bei additiver Fertigung nur die essentiellen Bereiche zu drucken.
Vergleich Zykluszeit von konturnaher und konventioneller Kühlung
Die angestrebte Jahresproduktion liegt bei 50.000 Formteilen. Die Zykluszeit der konventionellen Einsätze beläuft sich auf 38 Sekunden. Durch die Konstruktion konturnaher Kühlkanäle wird mit additiv hergestellten Werkzeugeinsätzen eine Kühlzeitreduktion um 60 % von 25 Sekunden auf 10 Sekunden und eine Zykluszeitreduktion um 39 % gegenüber Referenzteilen mit konventionell hergestellten Werkzeugeinsätzen erreicht.
Im Vergleich zu den konventionell hergestellten Werkzeugeinsätzen ergibt sich daraus eine Kosteneinsparung durch die niedrigeren Spritzgießkosten. Zudem können die benötigten Fertigungstage durch die kürzere Zykluszeit um mindestens acht Tage reduziert werden.
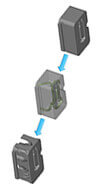
Topologieoptimierung = Kostenreduzierung
Mittels Topologieoptimierung konnte das Gewicht der Formeinsätze um 35 % von 2 kg auf ca. 1,5 kg reduziert werden.
Folglich reduziert sich die Maschinenzeit bei der additiven Fertigung, ohne Einbußen der mechanischen Eigenschaften, um ca. 30 %. Dadurch sparen Sie bares Geld!
Sie möchten wissen, wie Sie Ihre Produktionskosten mittels additiver Fertigung senken können?
Kontaktieren Sie uns für Fragen, Wünsche und Ideen, wir helfen Ihnen gerne.