Uddeholm Tyrax für die additive Fertigung
– Noch mehr Vorteile durch hohes Anlassen direkt nach dem Druck!
Die wirtschaftliche Verarbeitung moderner Kunststoffe im Spritzgussverfahren stellt hohe Anforderungen an die im Aktivbereich eingesetzten Werkzeugstähle. Durch zugesetzte Additive im Kunststoff kann es zu verschleiß- und korrosionsbedingten Ausfällen der formgebenden Bauteile kommen. Aus diesem Grund werden häufig Stähle eingesetzt, die eine ausreichende Korrosions- als auch Verschleißbeständigkeit aufweisen. Eine möglichst gute Polierbarkeit und eine hohe Zähigkeit runden das Eigenschaftsprofil ab. Um diesen Anforderungen zu begegnen, wurde unser Kunststoffformenstahl Uddeholm Tyrax ESR entwickelt. Dieser Premiumstahl hat sich mittlerweile bei vielen Anwendungen als erfolgreicher Problemlöser in der Kunststoffverarbeitung etabliert.

Zur weiteren Erhöhung der Produktivität haben sich in den letzten Jahren additiv gefertigte Bauteile mit konturnaher Kühlung bzw. Temperierung bewährt. Die Herstellung erfolgt durch das selektive Laserschmelzen eines Stahlpulvers im sogenannten LPBF-Verfahren (Laser-Powder-Bed-Fusion).
Mit dem für die additive Fertigung neu-entwickeltem Werkstoff „Tyrax für AM“ können wir unseren Kunden nun ein hoch-innovatives Stahlpulver und auf Wunsch auch komplett fertiggedruckte Bauteile mit einer einzigartigen Eigenschaftskombination anbieten.
Alle Werte in % | C | Si | Mn | Cr | Mo | V | N | O |
---|---|---|---|---|---|---|---|---|
Tyrax für AM LPBF-Pulverkorngröße: 20-50 µm | 0,40 | 0,2 | 0,5 | 12,0 | 2,3 | 0,5 | + | max. 0,02 |
Uddeholm Tyrax ESR | 0,40 | 0,2 | 0,5 | 12,0 | 2,3 | 0,5 | + | – |
Normalerweise werden additiv-gefertigte Werkzeugstähle nach dem Druckprozess einer Wärmebehandlung bestehend aus Härten und Anlassen unterzogen. Beim Tyrax für AM führt eine optimierte Wärmebehandlung, bestehend aus hohem Anlassen direkt nach dem Druckprozess, zu nochmals verbesserten Eigenschaften. Der Härteprozess entfällt somit vollständig. Bei hybriden Bauteilen empfehlen wir jedoch auf die klassische Wärmebehandlung in Form von Härten und Anlassen zurückzugreifen. Dabei werden Eigenschafften eingestellt, die nahezu identisch mit denen des Stabmaterials Uddeholm Tyrax ESR sind.
Verbesserte Korrosionsbeständigkeit durch direktes hohes Anlassen
Die durchgeführten Korrosionsversuche basieren auf der Messung von Stromdichte-Potential-Kurven. Bei dem verwendeten Elektrolyten handelte es sich um 0,1M NaCl-Lösung. Das Bild unten zeigt die relative Korrosionsbeständigkeit von AM Corrax sowie Tyrax für AM und 1.2083 (Stabmaterial) in verschiedenen Wärmebehandlungszuständen. AM-Corrax weist die höchste Korrosionsbeständigkeit auf. Im Vergleich dazu zeigt Tyrax für AM im hoch-angelassenem Zustand, direkt nach dem Drucken, die zweit-höchste Korrosionsbeständigkeit. Er übertrifft sogar die Korrosionsbeständigkeit des gehärteten und niedrig-angelassenen Wärmebehandlungszustandes der anderen Stähle. Dies bedeutet, dass die bisherigen Nachteile des gehärteten und niedrig-angelassenen Zustandes entfallen und der Vorteil der verbesserten Korrosionsbeständigkeit trotzdem genutzt werden kann. Als Nachteile des niedrig angelassenen Zustandes bei korrosionsbeständigen Werkzeugstählen sind zu nennen: Erhöhte ungünstige Eigenspannungen, Einschränkungen bei der Verarbeitungstemperatur und hoher Restaustenitgehalt sofern nicht vorher tiefgekühlt wird.
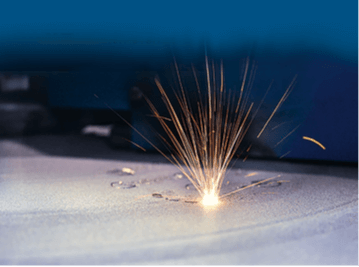
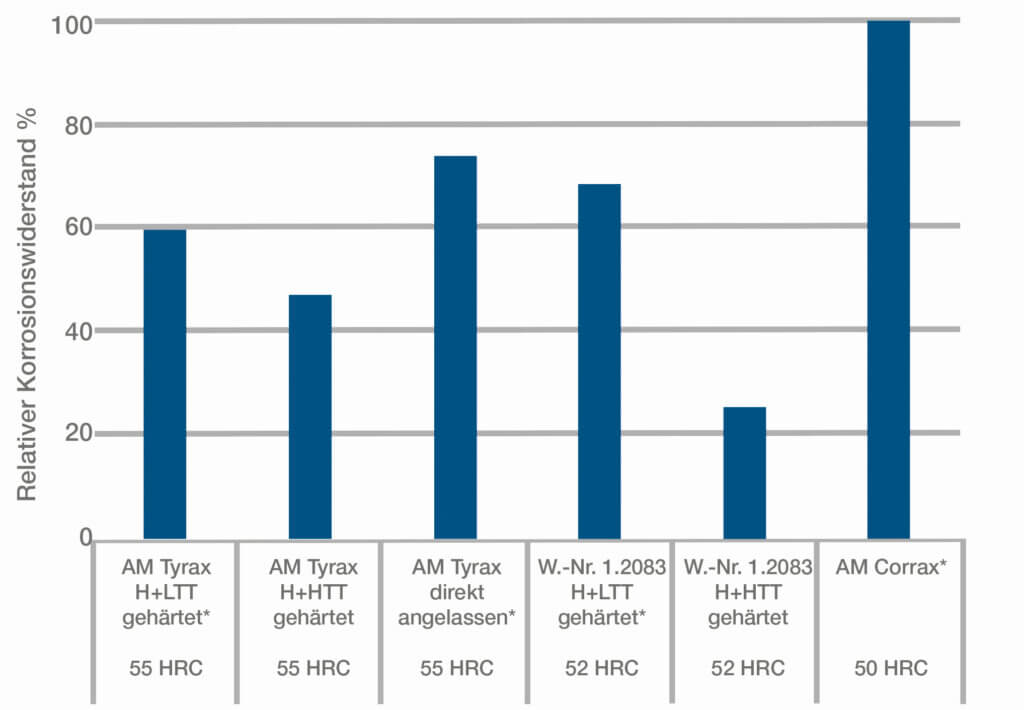
- AM Tyrax H+LTT gehärtet: Nach dem Drucken gehärtet (H=Hardening) und anschließend niedrig-angelassen (LTT=Low-Temperature-Tempering)
- AM Tyrax H+HTT gehärtet: Nach dem Drucken gehärtet (H=Hardening) und anschließend hoch-angelassen (HTT=High-Temperature-Tempering)
- AM Tyrax direkt angelassen: Nach dem Drucken wurde direkt hoch-angelassen
- W. Nr. 1.2083 H+LTT gehärtet: Gehärtet (H=Hardening) und anschließend niedrig-angelassen (LTT=Low-Temperature-Tempering)
- W. Nr. 1.2083 +HTT gehärtet: Gehärtet (H=Hardening) und anschließend hoch-angelassen (HTT=High-Temperature-Tempering)
- AM Corrax: Nach dem Drucken wurde Lösungsgeglüht und anschließend ausgelagert.
Bild links: Relative Korrosionsbeständigkeit für verschiedene Stähle und Wärmebehandlungszustände.
Verbesserte Zähigkeit durch direktes hohes Anlassen
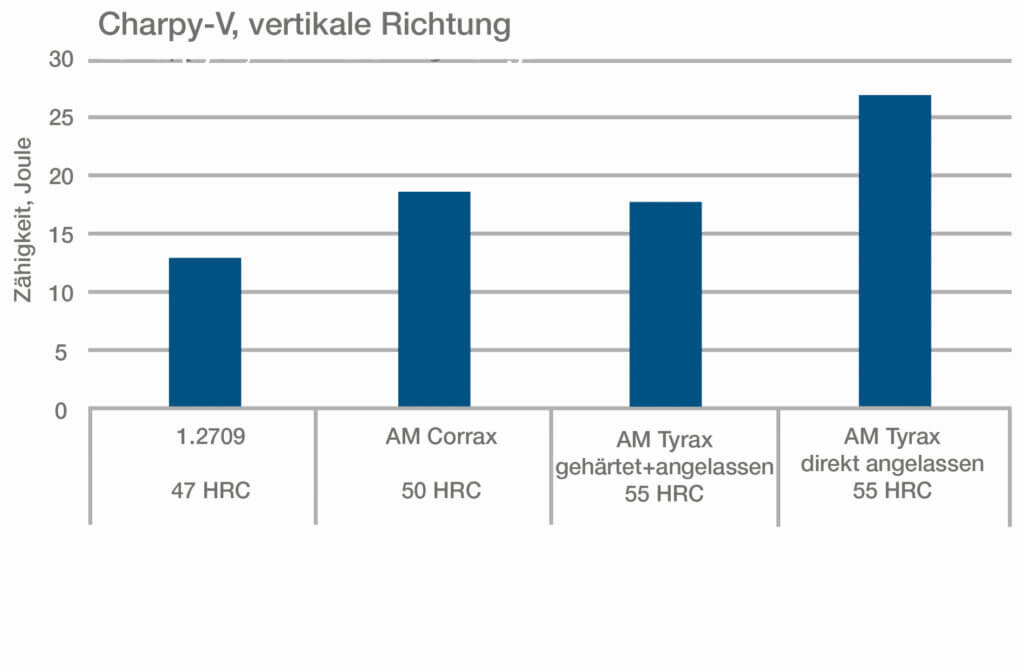
Das Bild links zeigt die in Kerbschlagbiegeversuchen gemessene Zähigkeit der gedruckten Uddeholm-Stähle AM Corrax und Tyrax für AM im Vergleich zum 1.2709.
Es ist zu erkennen, dass der nach dem Drucken direkt hoch-angelassene Tyrax für AM signifikant bessere Zähigkeitswerte aufweist.
Bild links:
Kerbschlagbiegearbeit (Charpy-V) von gedruckten Uddeholm-Stählen: AM Corrax, AM Tyrax.
Hoher Verschleißwiderstand durch direktes hohes Anlassen
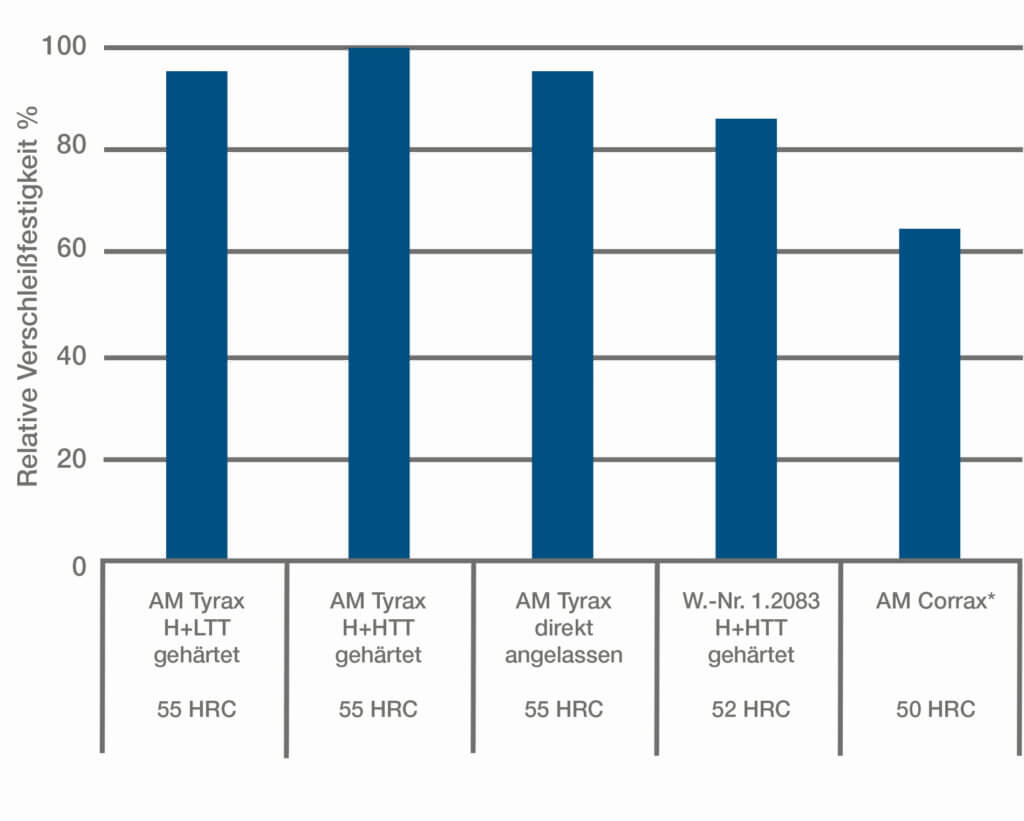
Die Messung des abrasiven Verschleißwiderstandes erfolgte in Pin-On-Disc-Tests gegen Korund-Schleifpapier (Al2O3). Anschließend wurde der Gewichtsverlust der Stahlproben ermittelt und auf den Werkstoff mit dem höchstem Verschleißwiderstand normiert.
Das Bild links zeigt die Ergebnisse des Tyrax für AM in verschiedenen Wärmebehandlungszuständen im Vergleich zu AM Corrax und 1.2083 (Stabmaterial). Der höchste Verschleißwiderstand wird vom gehärteten und hoch-angelassenem Tyrax für AM erzielt. Nur knapp dahinter folgt der nach dem Drucken direkt hoch-angelassene Tyrax für AM und der gehärtete und niedrig-angelassene Tyrax für AM. Im Vergleich zu einem 1.2083 und einem AM Corrax zeigt Tyrax für AM in allen drei Wärmebehandlungszuständen einen höheren Verschleißwiderstand.
Bild links: Relativer Verschleißwiderstand des gedruckten Tyrax für AM in verschiedenen Wärmebehandlungszuständen.
Fazit
Gedruckte und anschließend direkt hoch-angelassene Bauteile aus Tyrax für AM erzielen Härten bis 55 HRC und kombinieren in diesem Wärmebehandlungszustand so viele Vorteile wie kein anderer gedruckter Stahl:
- Nochmals verbesserte Zähigkeit gegenüber dem gehärteten und angelassenen Zustand
- Nochmals höhere Korrosionsbeständigkeit im Vergleich zum gehärteten und angelassenen Zustand
- Höherer Verschleißwiderstand gegenüber 1.2083 und AM Corrax
Haben Sie allgemeine oder technische Fragen zu diesem Artikel?
Kontaktieren Sie uns einfach, um mehr über Uddeholm Tyrax AM zu erfahren > hier geht es zum Kontaktformular »