Injection Moulding
Injection Moulding is the most commonly used method of producing plastic parts. It is a fast process and it is used to produce large numbers of identical items from high precision engineering components to disposable consumer goods. Examples are plastic parts that we find around us in our everyday lives, consumer goods like packaging of various kinds, and more technical items like mobile phones or electronic components.
Plastic as an engineering material is also increasing in importance in the automotive industry as it can:
- help to make the car lighter, thus reducing fuel demand and greenhouse gas emissions
- contribute to the quicker introduction of design innovations and changes
- provide single mould components which have helped to decrease vehicle assembly times
- improve the functionality of the cars as more technical polymers are developed
The moulds used for injection moulding are often extremely complicated and expensive. This is why the material used for the moulds often need to have unique characteristics for demanding applications. It is crucial to choose the correct steel grade for each specific type of mould. Different mould materials can be used depending on the number of shots, the plastic material being used, the size of the mould and the required surface finish. Several basic mould material properties must be considered: strength and hardness, toughness, wear resistance, cleanliness, corrosion resistance and thermal conductivity.
Uddeholm has long been leading the innovation of new steel grades to secure the requisite properties. Our ESR materials for high surface finish demands are renowned in the industry, as is our Uddeholm Stainless Concept, comprising corrosion resistant grades for reduced mould maintenance.
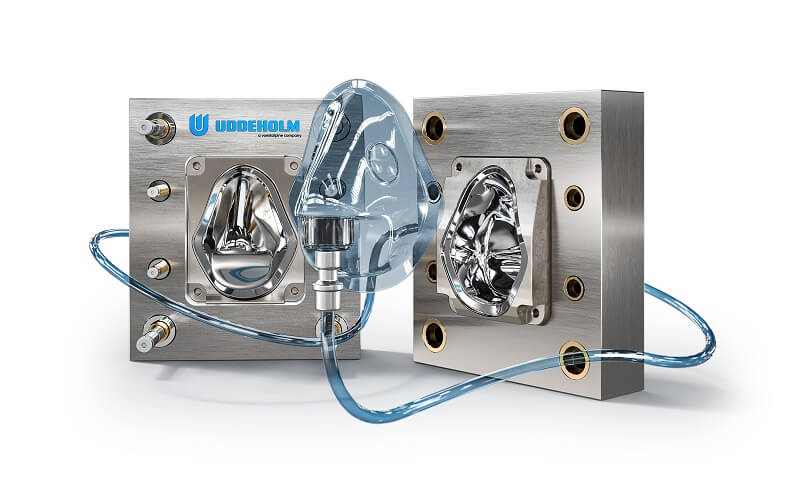
ALL TOOL STEEL FOR INJECTION MOULDING
- Alumec 89
- Uddeholm Caldie
- Uddeholm Corrax
- Uddeholm Dievar
- Uddeholm Elmax SuperClean
- Uddeholm Formvar
- Uddeholm Impax Supreme
- Uddeholm Mirrax 40
- Uddeholm Mirrax ESR
- Uddeholm Nimax
- Uddeholm Nimax ESR
- Uddeholm Orvar 2 Microdized
- Uddeholm Orvar Supreme
- Uddeholm Orvar Supreme
- Uddeholm Polmax
- Uddeholm QRO 90 Supreme
- Uddeholm Rigor
- Uddeholm Stavax ESR
- Uddeholm Tyrax ESR
- Uddeholm Unimax
- Uddeholm Unimax
- Uddeholm Vanadis 4 Extra SuperClean
- Uddeholm Vanax SuperClean
- Uddeholm Vidar 1 ESR