Compression and Transfer Molding Tool Steel
Compression molding
Compression molding is a technique mainly for thermoset molding and is often used for molding of glass fibre reinforced plastic. In the process the molding compound is placed in the open mold cavity, the mold is closed and heat and pressure are applied until the material is cured. High hardness steel is normally used. For big molds it is common to use prehardened material with high hardness inserts, in places where higher wear resistance is needed.
Mold material properties
Important properties are:
- Wear resistance
- Strength and hardness
Transfer molding
Transfer molding is a method of molding thermosetting materials and is very common in production of electronic devices such as integrated circuits, capacitors and diodes. In the process the plastic is softened by heat and pressure in a transfer chamber, then forced by high pressure through sprues, runners and gates into a closed mold for final curing. An important advantage with this method is the close dimensional tolerances possible to achieve.
Mold material properties
The resin, especially epoxy, tends to attack the mold and the part may stick in the mold during ejection. Often some type of surface treatment is needed. In order to avoid indentations the compressive strength should be high. Bigger inclusions in the mold material must be avoided, as it may give an imperfect surface. Because of the very strict tolerances of the part the mold inserts must have a very good dimensional stability during production.
The different components of an IC mold each have individual demands on the tool material. Each component requires steel with a suitable properties profile. The following properties are important:
- Wear resistance
- Compressive strength
- Corrosion resistance
- Cleanliness
- Dimensional stability during use
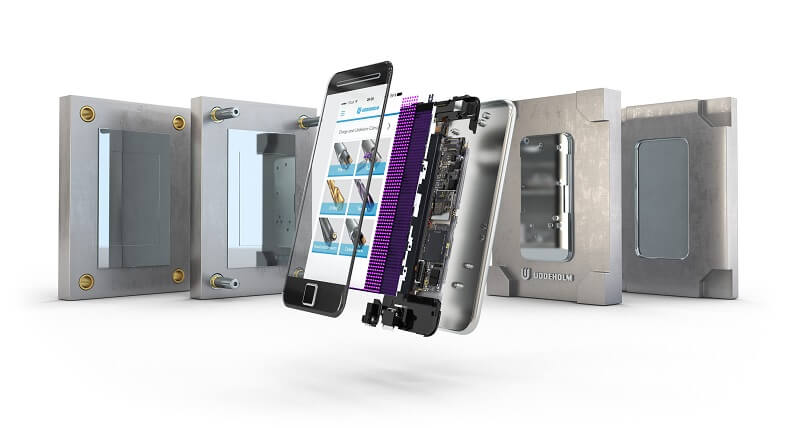